Sheffield 3D printer develops new process to help detect issues in food production
Addition Design, based at the Advanced Manufacturing Park Technology Centre, has designed a process which allows food manufacturers to access production parts that meet the regulatory requirements of food production components.
Tom Fripp, director at Addition Design, said: “We’re incredibly proud to have found a solution that works for all parties and, importantly, reduces the costs for food manufacturers. The particular process we have developed means that we can produce parts on demand for manufacturers, using our Selective Laser Sintering machine and then post-process them in a way that means they still meet food contact requirements."
Advertisement
Hide AdAdvertisement
Hide AdThe new technique addresses a number of issues that affect the industry’s ability to use 3D printing while complying with food-safety regulations which require food contact components to be blue.

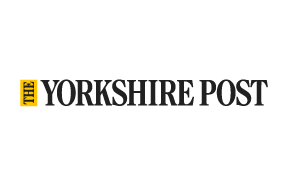
Components on food production lines are traditionally made blue in order for them to be easily identified if they fail or brake, so to keep them out of any final food products. This requirement has previously acted as a barrier for 3D printing, as there are few ways to make cost-effective, high-quality certified, blue food contact parts using industrial 3D printing. The new process was created by Addition Design exclusively for AddParts.