Modular housing potential for older people is often overlooked - Tony Tench
High-quality precision and shorter construction timelines are the main benefits often associated with adopting alternative house building methods like modular. However, for Housing 21 we also saw the opportunity to provide homes that minimise our environmental impact, maximise energy efficiency and reduce running costs for our residents.
Located off Cooke Street in Bentley, Patent Walk and Patent House is the first scheme delivered to meet our ‘low-carbon specification’, which far exceeds current building regulations – achieving the Future Homes Standard and 2050 net-zero target.
Advertisement
Hide AdAdvertisement
Hide AdConstructed by M-AR Off-Site at its factory in Hull, the scheme is a development of 20 homes, including eight bungalows and 12 apartments, for older people, available for social rent.

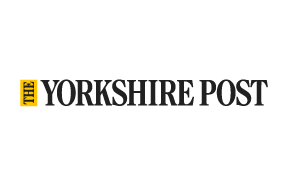
Built using volumetric modular construction – where large, enclosed, pre-made and fitted-out sections are joined together on-site to form a complete building – the new homes are fitted with mechanical ventilation with a heat recovery system that supplies and extracts air to reduce the heating and cooling needed throughout the building.
Of course, this isn’t the only technology integrated into the homes for the benefit of residents and the environment. Across the scheme electric vehicle (EV) charging points, photovoltaic (PV) solar panels and air source heat pumps have also been installed.
As part of the project, we were also able to install solar panels on the roof of a neighbouring Housing 21 scheme, Minden Court, enabling us to produce more renewable energy for the wider complex and reducing costs further for residents.
Advertisement
Hide AdAdvertisement
Hide AdDuring the manufacturing process circular economy principles were adopted. This included ensuring any waste generated on the production line was either recycled or reused and specifying that the module frames were fabricated from volumetric lightweight steel, which can be easily recycled at the end of the building's life.
Completion of this scheme is a huge milestone for Housing 21, but we know the work doesn’t end here. Patent Walk and Patent House is the third project we’ve delivered with M-AR and modular consultant and employer’s agent, Henry Riley. Across our projects to date, we’ve worked together to carefully hone our design to unlock the full potential of off-site construction in helping to achieve net zero energy efficient housing.
This has included assessing the way the modules were constructed, delivered and installed, as well as considering the operational costs and the whole lifecycle of the building and its component materials.
We have already put in place a year-long programme to accurately monitor the energy use of Patent Walk and Patent House, so we can assess how well they work for residents in practice.
Advertisement
Hide AdAdvertisement
Hide AdOur plan is to then review this information alongside another traditionally built scheme, so we can capture data that will further shape net zero homes of the future.
Tony Tench is deputy chief executive at Housing 21.